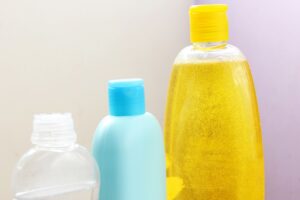
Consider these factors to find the best liquid packaging machines for your needs.
Liquid filling systems are designed to accommodate a variety of different liquid viscosities and characteristics, and there is no one-size-fits-all system. The exact system you end up using will depend on a variety of factors, particularly factors like fill temperature and pressure, product size, and automation. The liquid packaging and filling experts at Filamatic can help you find the best equipment for your facility and production needs.
Fill Temperature Management
Managing the temperature of a liquid as it is packaged is essential for several reasons. When filling beverages, for example, keeping a liquid within a designated temperature range is critical for preserving the taste and freshness of the liquid. Furthermore, the temperature can impact the viscosity of many liquids. For example, some liquids remain easily pourable at a high temperature but become much thicker when cooled. The best liquid filling system for your facility will allow you to determine the temperature at which your product is poured for the best results.
Control Fill Pressure
The pressure must be controlled for many liquid products, especially carbonated beverages. In those instances, too much pressure can lead to the drink bubbling and foaming up and over the container. Investing in a liquid packaging system that allows pressure control is essential for spill prevention and consistent products.
Consider Packaging Size
When packaging liquids, you must also account for your container size. The container should be slightly larger than the volume, as natural changes in temperature may cause the liquid to expand. If you do not allow that extra “breathing room” for the liquid product, it may burst or overflow after being filled or during transport to the consumer.
Automated vs. Semi-Automated Filling Systems
When creating your liquid packaging system, you must consider whether automated or semi-automated systems are best. All liquid packaging systems can speed up the production line. When your system is fully automated, the containers can move along a conveyor belt through filling, capping, and labeling stations.
Semi-automated systems are often best for facilities with lower production rates. These systems often require a person to place the bottle under the filling machine, put the cap on, and use a manual interface to seal the container.
Specialists in Liquid Filling Systems
For over 70 years, FILAMATIC has provided a wide range of liquid filling machines to the packaging market. We create flexible, customized solutions for every stage of your business growth. Whether you require a single machine, a complete turnkey fill-cap-label solution, or a fully automated, integrated Monobloc system, we have the liquid filling experience for your project.
For more information on liquid filling, capping, and labeling solutions, please call 866.258.1914 or visit – www.filamatic.com/contact-us.