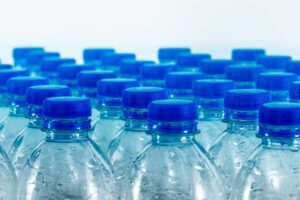
Consider these factors when selecting the best capping machine for your production line.
Finding the best liquid filling machine for your production line can be difficult on its own. However, you also need to consider what equipment you need for the rest of your production line. Most notably, a capping machine will be essential for packaging efficiency. Finding a great capping machine doesn’t depend on quite as many factors, but you should still carefully consider your options before making your choice. You should consider the following factors when selecting the best capping machine for your specific requirements.
The Range of Cap Sizes
Caps for containers range in size from 5 mm to 120 mm in diameter. If your cap sizes vary wildly, you may need to install more than one capper to meet your product needs. Capping machines for larger caps may require installing a vertical placing device along with a cap tightener. Capping for small caps may need a “monobloc” system that maneuvers bottles in a starwheel formation.
You may also need to consider a sorting system based on the size of the caps. Small caps may need a vibratory sorting system, while large caps often use large bulk elevator sorting machines.
The Cap Shapes
The width-to-height ratio of the cap will influence the cap sorting option and the type of capping machine to use. Flat caps with larger widths than heights are among the easiest to apply and are compatible with almost every capping machine. However, if your caps are taller or more square, your options may be limited to centrifugal or vibratory machines.
Caps of different shapes may require vertical placement or a cap chute. The geometry of the cap will determine when you should use a vertical chuck capper or an inline capper.
If your container uses a more particular closure, such as a dropper tip, spray head, or a pump, an automatic tightener is often used instead of a capping machine.
Cap Fit and Design
Some threaded closures, such as spout caps, are incompatible with many capping machines. They will require the chuck-type capping machine, in addition to vertical placement devices. These caps contain a skirt that needs to fit into the mouth of the container before engaging threads for tightening. This method applies to other closures such as corks, stoppers, and plugs.
Vertical capping machines operate intermittently, so they are often less efficient than inline continuous motion machines. Smaller businesses may find that smaller closures requiring monobloc systems are more expensive to install, hindering the profitability of many applications.
The Level of Efficiency
When finding your capping machinery, you should also consider what level of efficiency you desire. Do you prefer manual, semi-automatic, or automatic systems?
Manual capping includes applying and tightening by hand, which can be labor-intensive and less efficient. Semi-automatic cappers are more efficient, producing an average of 15 to 20 caps per minute. Fully automatic cappers and tighteners, depending on the application, can cap close to 200 CPM or higher.
The Packaging Environment
Your packaging environment will also influence your decisions when selecting your capping machine. If you work in a corrosive atmosphere or a facility with flammable substances, you will need machinery designed to work in these environments.
Your new capping machine should be able to fit in with your existing packaging environment and production line. Once you’ve found the best machine, you can start benefiting from its efficiency
Liquid Filling Experts
For over 70 years, FILAMATIC has provided a wide range of liquid filling machines to the packaging market. We create flexible, customized solutions for every stage of your business growth. Whether you require a single machine, a complete turnkey solution, or a fully-automated, integrated Monobloc system, we have the liquid filling experience that will exceed your expectations.
For more information on liquid filling, capping and labeling solutions, please call 866.258.1914 or visit – www.filamatic.com/contact-us.