In the liquid filling business, you deal with unique applications that require specific solutions. Whether due to product or environment, some of these different applications require explosion resistant machinery. Explosion resistant solutions can be an incredibly complex and involved area; however, for our purposes here today, we will highlight general points, or areas of discussion that we believe important.
What does “Explosion Resistant” mean, and when do you need one?
In an in-depth discussion with Jack Grosskopf, FILAMATIC’s Director of Engineering, he shares his thoughts on what you need to know about explosion resistant liquid filling equipment. What does Explosion Resistant mean?
“Explosion Resistant” can have different meanings to different people. If you go by the textbook definition of “Explosion Proof Apparatus” from the National Fire Protection Agency’s (NFPA), an international codes and standards organizations, which publishes the National Electrical Code (NEC) handbook, it reads;
Apparatus enclosed in a case that is capable of withstanding an explosion of a specified gas or vapor which may occur within it and of preventing the ignition of a specified gas or vapor surrounding the enclosure by sparks, flashes, or explosion of the gas or vapor within, and which operates at such an external temperature that a surrounding flammable atmosphere will not be ignited thereby.
Jack quickly states, “To put this into regular speak, explosion resistant is a classification where there is a risk of a fire or explosion from gas, fumes, vapors or materials in the air around surrounding a machine or being handled by it. The materials, components, and machine design is built so that it will prevent an explosion or fire in case of a spark igniting gas, fumes, or the liquid product itself.”
What goes into an Explosion Resistant machine?
“The short answer, it’s the same type of equipment that goes into an explosion resistant liquid filling machine compared to non-explosion resistant machine – this includes the motors, sensors, conveyors, etc.”, says Jack. However, the components and parts used within an explosion proof machine are much different in design. That is, FILAMATIC uses intrinsically-safe input-output devices, sensors and monitoring devices, on explosion resistant equipment.
What does intrinsically-safe mean? Again the textbook definition, Possessing not incendiary characteristics. Usually related to not having the capability to store energy. In other words, “intrinsically-safe” is a term we can use when a machine component doesn’t produce enough power to cause a spark. Anytime you add power, amps and volts, it cannot be intrinsically-safe.
Unfortunately, we are limited by the amount of intrinsically-safe sensors and monitoring devices available on the market. There are roughly 200 possible sensor options for a standard liquid filling machine, these options dwindle down to 3 intrinsically-safe sensors that can be used on explosion resistant machines.
Motors installed on machines may not be intrinsically-safe since a motor needs to produce a sufficient amount of power to operate. Any motor that will do a sufficient amount of work will exceed the power requirements of an “intrinsically-safe” device.
Explosion resistant motors are built to withstand sparking and won’t let gas, fumes, or vapors inside. If there is somehow an explosion inside the motor, it will be contained. Devices and power components, intrinsically-safe or not, are all made for the class group and division you are running the machine in. Other materials used on an explosion resistant machine include statically-resistant lexan, poly-carbonate. anti-static conveyor systems, etc.
When would you need an Explosion Resistant machine?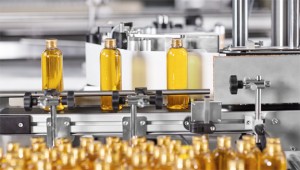
The NFPA uses “ hazardous” as a definition to designate when an explosion resistant machine is necessary.
Hazardous in the NEC handbook means a location, area, or space where fire or explosion hazards may exist due to gases, vapor, ignitable liquids, combustible dust, or flammable fibers. Whether a work area or factory environment is considered “hazardous” is by the determination of an insurance company, not by an equipment manufacturer.
Now the chemical compound of the product is an important consideration. Some everyday households items that you use might surprise in learning that they are flammable, nail polish, non-dairy creamer, hand sanitizer, some flours, and even deodorant. You can always check the Material Safety Data Sheet (MSDS) to understand how likely it is to cause a fire concern.
The specific chemical, stored location, and individualized amounts are important considerations as well for explosion resistant machines. For instance small amounts of nail polish are not a huge concern. However, large amounts of solvent in a factory and production environment, can be a major concern.
Regarding the liquid filling side of things, you would focus on material classification. Class one which means gases and vapors. FILAMATIC builds liquid filling equipment to the specifications of Class 1 Division 1 from the NEC handbook. Following best practices would always encourage you to speak with an insurance company about what is and what is not a hazardous environment. Typically this is not something that is determined for a customer.
Jack closes by saying, “there are many variations of explosion resistant machines, and what I have learned over the years within the liquid filling industry, specific design features are also determined by various application factors, not limited to, but also including the location of the machine, product properties being handled, and believe it or not, even the different types of containers/bottles that are being filled.”
Liquid Filling Machine Specialists
For more information on FILAMATIC’s liquid filling solutions, please call 866.258.1914 and ask for Customer Service, or simply email info@filamatic.com.